Online Class: Introduction to Six Sigma
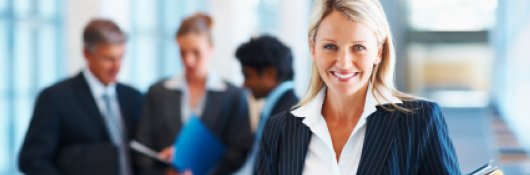
no certificate
with CEU Certificate*
-
15Lessons
-
22Exams &
Assignments -
2,555Students
have taken this course -
9Hours
average time -
0.9CEUs
Course Description
Mastery of Six Sigma Principles
Six Sigma stands tall as a robust methodology, central to ensuring projects achieve their pinnacle of success. Rooted in principles that champion excellence, Six Sigma is built on a rich tapestry of time-tested best business practices. The ultimate aspiration of this approach? Crafting an operational milieu that is almost devoid of errors.
The intriguing moniker 'Six Sigma' derives from the Greek letter sigma, traditionally employed by mathematicians to gauge variability. Translating this to the business arena, variability becomes a yardstick for assessing errors within processes. Striving for perfection, Six Sigma aims to achieve an outstanding rate of fewer than 3.4 glitches for every million transactions, where a transaction can be visualized as a tangible product manufactured or a service executed.
The success story of Six Sigma lies in its evolutionary nature. By eliminating the redundancy inherent in preceding business methodologies, it has ascended to an esteemed pedestal, revered as a top-tier project management system. Prestigious global corporations vouch for Six Sigma's principles, driven by a contemporary business landscape where consumers are no longer content with mediocrity. They demand unparalleled excellence, compelling enterprises to raise their game in a market teeming with rivals.
Our course is a comprehensive tapestry, intricately weaving the core aspects of Six Sigma, designed to equip you with the knowledge and skills to don the prestigious mantle of a 'Black Belt'—an esteemed Six Sigma team player.
Detailed Course Outline
-
History of Six Sigma: Delve deep into the origins of this methodology. Understand how it has evolved over the years, drawing examples from pioneering companies that adopted and benefitted from it.
-
Implementing Six Sigma: Gain insights into the practical aspects of embedding Six Sigma principles into a business framework, spotlighting real-world success stories.
-
Becoming a Customer and Market-Driven Enterprise: Understand the pivotal role of customers. Learn strategies that pivot businesses around market demands, underpinned by illustrative case studies.
-
Customer Expectations and Needs: Dive into the psyche of the modern consumer. Decode their aspirations, needs, and expectations to tailor products and services that resonate.
-
Linking Six Sigma Projects to Strategies: Harness the power of strategic alignment. Explore how Six Sigma projects can be seamlessly integrated with overarching business strategies.
-
Attributes of Good Metrics: Metrics are the compass guiding businesses. Discover the characteristics of effective metrics that facilitate informed decision-making.
-
Using Resources Wisely: Master the art of resource optimization. Learn how to allocate and utilize resources efficiently, maximizing ROI.
-
Project Management Using the DMAIC and DMADV Models: Grasp these core Six Sigma models. Understand their nuances and applications, enriched by engaging case studies.
9-11. Define, Measure, and Analysis Phases: These modules dissect the first three phases of the DMAIC model. From defining problems to measuring metrics and analyzing data, understand the intricate steps that drive project success.
12-13. Analyzing Data Modules: Comprehend the art of data analysis. Whether it's streamlining value streams or experimenting with designs, these lessons emphasize data-driven decision-making.
14-15. Improve and Control Phases: The culmination of the DMAIC model. Learn how to implement improvements and establish controls to maintain those enhancements.
Why This Course?
Six Sigma, with its potent blend of analytics, strategies, and customer-centricity, is not just a methodology—it's a philosophy. In a world where competition is fierce, and customer loyalty is gold, embracing Six Sigma can be a game-changer.
Our course is not a mere academic exercise; it's a journey. A journey filled with insights, real-world examples, and hands-on exercises. By its conclusion, you'll not only comprehend the theoretical nuances of Six Sigma but be adept at applying them in real-world scenarios.
In a marketplace that rewards excellence, equip yourself with the tools to not just survive, but thrive. Dive into the world of Six Sigma with us, and chart a course to unparalleled professional success.
Course Motivation
The employees within a company who train on Six Sigma are called "Six Sigma Black Belts." Usually, these Black Belts use advanced computer and business technologies, but the methodology of Six Sigma can easily be broken down to a simple model that comprises five elements: Define, Measure, Analyze, Improve, and Control. Together, they are referred to as the DMAIC model.
Using the DMAIC model, a company's Black Belts must define (D) the goals of a project, measure (M) the existing system in place, analyze (A) the implementation of the project to ensure that there is little difference between actual results and the goals of the project, improve (I) the system wherever possible, and, finally, they must control (C) the new system in place to ensure continued success.
History of Six Sigma
The concepts of Six Sigma were created by the company Motorola in the 1980s under the leadership of Bob Galvin, the company's Chief Executive Officer (CEO). In the early 1970s, a Japanese company took control of a Motorola factory that manufactured televisions. The quality of the televisions was very low and Motorola hired a firm to investigate the problems and to implement a solution.
Within a very short period of time after the Japanese firm took control, the quality of the televisions was dramatically improved. Defects were decreased by 95%, but the company used the same workers and the same technology. In addition to drastically lowering defects, the company was also able to lower manufacturing costs. One thing was very clear: Motorola's management of the factory was the problem and the Japanese firm had managed the process with a remarkable degree of success. The concepts they used to achieve this success were incorporated and expanded by Motorola and would eventually become known as Six Sigma. In 1988, Motorola won the prestigious Malcolm Baldrige National Quality Award, one of the most coveted awards in business. Other businesses started to take notice of Motorola's success and strategy, and the concept of Six Sigma grew rapidly.
One of the most fundamental concepts to understand about Six Sigma is that its methodology is not solely concerned with increasing quality in the traditional sense. While increased quality is a result of its implementation, Six Sigma is primarily concerned with increasing efficiency within a company and delivering higher customer value.
Six Sigma is not solely about cutting costs to improve the bottom line. It is about cutting unnecessary expenses (waste) which do not add to the actual quality, or value, of its products. When companies spend money to fix problems, this expense is often called the cost of poor quality. Typically, companies that utilize Six Sigma spend about 5 percent of the their revenue fixing problems, while the typical cost in most companies that do not use Six Sigma can be as high as 25 percent of revenue.
The Scientific Method
Six Sigma applies the Scientific Method to business. The Scientific Method is a very precise approach used by scientists to invent, discover, and test their theories. Any discovery or theory that does not closely follow the Scientific Method is not regarded as a valid experiment.
The principles of Six Sigma follow these important elements of the Scientific Method:
- Observation: Closely examine the operations of your business.
- Draft an explanation, or theory, that summarizes your observation.
- Develop predictions of future events based on your observations and theory.
- Make experiments to test your predictions. Adjust your theory, if necessary, based on your experiments.
- Repeat the process of developing predictions and conducting experiments until there are no differences between your theory and the results of your experiments.
At the end of this process, a Black Belt in a Six Sigma company will be detailed to certify a theory which explains an important element of the company's business. It eliminates a culture of guessing and employee bickering and moves to a more factual environment.
Six Sigma versus Older Project Management Methodologies
There have been many process and quality improvement initiatives used before Six Sigma, but they differ in several important ways.
Traditional process improvement initiatives focused almost exclusively on the manufacturing process while Six Sigma is concerned with the analysis of data across a broad spectrum of a business. It analyzes all aspects of the business environment, with a special emphasis on efficiency. Thus, Six Sigma considers manufacturing just one part of the business process since customers are concerned about many more things than just the manufacturing quality of a product.
In addition to wanting a high quality manufactured product, customers are concerned with price, service, keeping updated with future releases of the product, and technical support, among many other concerns.
The beneficial effects of this approach go far beyond just customers. Investors and owners benefit greatly from Six Sigma as it improves the bottom line performance of the company. All stakeholders, which are defined as people who have an interest in the success of the company, benefit from the Six Sigma approach to improving efficiency and adding value to the customer experience.
- Completely Online
- Self-Paced
- Printable Lessons
- Full HD Video
- 6 Months to Complete
- 24/7 Availability
- Start Anytime
- PC & Mac Compatible
- Android & iOS Friendly
- Accredited CEUs
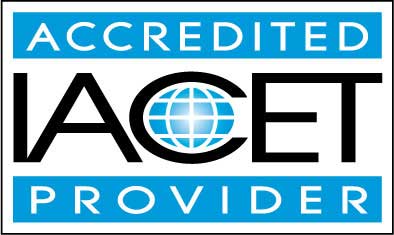
Course Lessons
Lesson 1. History of Six Sigma
Lesson 1 Video
Lesson discussions: Six Sigma; Reasons for Taking this Course
Complete: Lesson 1 Assignment
Complete Assignment: An Introduction
Assessment: Lesson 1: History of Six Sigma
Lesson 2. Implementing Six Sigma
Lesson 2 Video
Lesson discussions: Using Six Sigma
Complete: Lesson 2 Assignment
Assessment: Lesson 2 : Implementing Six Sigma
Lesson 3. Becoming a Customer and a Market Driven Enterprise
Lesson 3 Video
Complete: Lesson 3 Assignment
Assessment: Lesson 3: Becoming a Customer and Market-Driven Enterprise
Lesson 4. Customer Expectations and Needs
Lesson 4 Video
Complete: Lesson 4 Assignment
Assessment: Lesson 4: Customer Expectations and Needs
Lesson 5. Linking Six Sigma Projects to Strategies
Lesson 5 Video
Complete: Lesson 5 Assignment
Assessment: Lesson 5: Linking Six Sigma Projects to Strategies
Lesson 6. Attributes of Good Metrics
Lesson 6 Video
Assessment: Lesson 6: Attributes of Good Metrics
Lesson 7. Using Resources Wisely
Lesson 7 Video
Assessment: Lesson 7: Using Resources Wisely
Lesson 8. Project Management Using the DMAIC and DMADV Models
Lesson 8 Video
Assessment: Lesson 8: Project Management Using the DMAIC and DMADV Models
Lesson 9. The Define Phase
Lesson 9 Video
Assessment: Lesson 9: The Define Phase
Lesson 10. The Measure Phase
Lesson 10 Video
Assessment: Lesson 10: The Measure Phase
Lesson 11. Measurement System Analysis
Lesson 11 Video
Assessment: Lesson 11: Measurement System Analysis
Lesson 12. Analyzing Data: Value Streams and Dealing with Variations
Lesson 12 Video
Assessment: Lesson 12: Analyzing Data: Value Streams and Dealing with Variations
Lesson 13. Analyzing Data: Designed Experiments
Lesson 13 Video
Lesson discussions: Statistics
Assessment: Lesson 13: Analyzing Data: Designed Experiments
Lesson 14. The Improve Phase
Lesson 14 Video
Assessment: Lesson 14: The Improve Phase
Lesson 15. The Control Phase
Lesson 15 Video
Lesson discussions: End of Course Poll; Program Evaluation Follow-up Survey (End of Course); Course Comments; Course Comments
Assessment: Lesson 15: The Control Phase
Assessment: The Final Exam
Learning Outcomes
- Describe the history of six sigma.
- Summarize implementing six sigma.
- Describe becoming a customer and a market driven enterprise.
- Define customer expectations and needs.
- Determine how to link six sigma projects to strategies.
- Recognize attributes of good metrics.
- Describe using resources wisely.
- Summarize Project Management Using the DMAIC and DMADV Models.
- Identify the define phase.
- Identify the measure phase.
- Summarize Measurement System Analysis.
- Describe analyzing data: value streams and dealing with variations.
- Describe analyzing data: designed experiments.
- Identify the improve phase.
- Identify the control phase.
- Demonstrate mastery of lesson content at levels of 70% or higher.
Additional Course Information
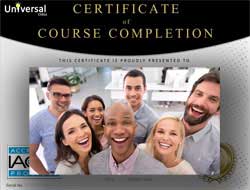
- Document Your Lifelong Learning Achievements
- Earn an Official Certificate Documenting Course Hours and CEUs
- Verify Your Certificate with a Unique Serial Number Online
- View and Share Your Certificate Online or Download/Print as PDF
- Display Your Certificate on Your Resume and Promote Your Achievements Using Social Media
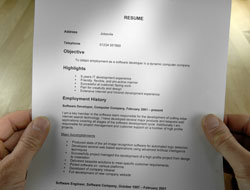
Choose Your Subscription Plan
No Certificate / No CEUs
This course only
Includes certificate | X |
Includes CEUs | X |
Self-paced |
![]() |
Instructor support |
![]() |
Time to complete | 6 months |
No. of courses | 1 course |
Certificate & CEUs
This course only
Includes certificate |
![]() |
Includes CEUs |
![]() |
Self-paced |
![]() |
Instructor support |
![]() |
Time to complete | 6 months |
No. of courses | 1 course |
Certificates & CEUs
Includes all 600+ courses
Includes certificate |
![]() |
Includes CEUs |
![]() |
Self-paced |
![]() |
Instructor support |
![]() |
Time to complete | 12 Months |
No. of courses | 600+ |
Certificates & CEUs
Includes all 600+ courses
Includes certificate |
![]() |
Includes CEUs |
![]() |
Self-paced |
![]() |
Instructor support |
![]() |
Time to complete | 24 Months |
No. of courses | 600+ |
Student Testimonials
- "The course was extremely helpful to jump-start my understanding of Six Sigma methodologies; the writing assignments were a great tools to synthesize the readings content. The extra readings added needed peripheries and helped me appreciate the breadth of the six Sigma applications and the flexibility of the system." -- Houssam E.
- "I learned a lot from this course and found it to be very helpful. I liked that the course materials could be printed and that the videos were captioned so the course was very accessible." -- Audrey C.
- "Excellent course. Great instructor." -- Shelly B.
Related Courses
-
32 hours 3.2 CEUs Microsoft Office: Word, Excel, PowerPoint and Outlook + More Info
-
29 hours 2.9 CEUs Human Resources Productivity Course Bundle + More Info
-
54 hours 5.4 CEUs Become a Life Coach - Course Bundle + More Info
-
36 hours 3.6 CEUs Ultimate Secretary Training Bundle + More Info
-
87 hours 8.7 CEUs Writing Help Course Bundle + More Info
-
6 hours 0.6 CEUs General Receptionist + More Info
-
12 hours 1.2 CEUs Business Math 101 + More Info
-
7 hours 0.7 CEUs Personal Communication Skills Level 4 + More Info
-
7 hours 0.7 CEUs How to Deal with Difficult Personalities + More Info
-
6 hours 0.6 CEUs Business Branding 101 + More Info
-
8 hours 0.8 CEUs Motivational and Public Speaking 101 + More Info
-
7 hours 0.7 CEUs Leadership Skills for Managers + More Info
-
7 hours 0.7 CEUs Time Management 101 + More Info
-
7 hours 0.7 CEUs Healthy Relationships + More Info
-
11 hours 1.1 CEUs How to Write Effective Policies and Procedures + More Info
-
6 hours 0.6 CEUs Managing Your Career + More Info
-
12 hours 1.2 CEUs Writing Effective Persuasion + More Info
-
5 hours 0.5 CEUs Communicating with Diplomacy and Tact + More Info
-
5 hours 0.5 CEUs Team Building 101 + More Info
-
12 hours 1.2 CEUs Advertising, Marketing and Sales Writing + More Info
-
5 hours 0.5 CEUs Creative Thinking Skills + More Info
-
5 hours 0.5 CEUs Habits of Millionaires + More Info
-
12 hours 1.2 CEUs How to Write Case Studies + More Info
-
11 hours 1.1 CEUs Business Consulting 101 + More Info
-
7 hours 0.7 CEUs Business Analysis + More Info
-
5 hours 0.5 CEUs Mastering Conversation Skills + More Info
-
19 hours 1.9 CEUs Business Writing + More Info
-
7 hours 0.7 CEUs Lean Management + More Info
-
5 hours 0.5 CEUs Workplace Safety + More Info
-
8 hours 0.8 CEUs Procurement Management + More Info
-
7 hours 0.7 CEUs Effective Communication Skills + More Info
-
6 hours 0.6 CEUs Delegation Skills + More Info
-
8 hours 0.8 CEUs Human Resources Management 101 + More Info
-
9 hours 0.9 CEUs Introduction to Six Sigma + More Info
-
5 hours 0.5 CEUs Business Etiquette + More Info
-
6 hours 0.6 CEUs Personal Assistant 101 + More Info
-
6 hours 0.6 CEUs Sustainable Development for Business + More Info
-
6 hours 0.6 CEUs Gender Sensitivity Training + More Info